Green' builders use environment gently in building efficient house
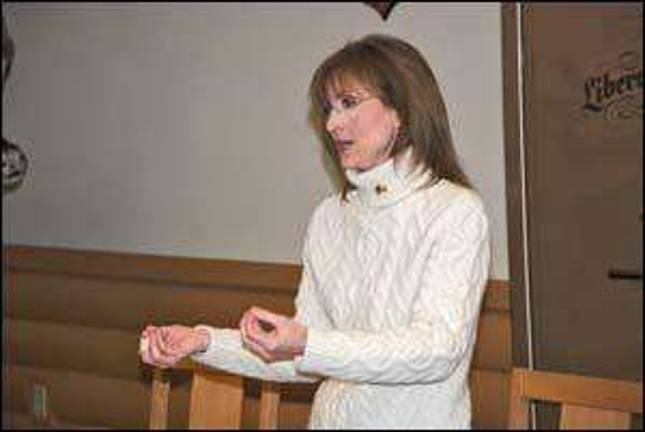
Warwick While most of us are doing our part to cut down on pollution and help put the brakes on global warming, some are taking the environment into account when building homes from the ground up. Take George and Glenn Rhein. These builders, located in Amity, are constructing homes to meet a “green” criteria. What constitutes a green building? Generally, green buildings are sited, designed, constructed and operated to enhance the well-being of its occupants and to minimize negative impacts on the community and natural environment. Green buildings increase the efficiency of energy, water, and materials used while reducing the impact on health and the environment. What the Rheins have done is both beautiful and efficient, according to Ernest Schlesinger, a realtor with Mason Samett Associates. “Everything you could possibly think of has been put into this house to lessen the impact on the environment and to make it more efficient,” said Schlesinger while giving a tour of the first of six homes being built off Amity Road. “There are no leaks anywhere. They caulk the plywood sheet edges where they meet. Every little thing that can make it more efficient, they’re doing it.” Heating costs cut in half This house is nearly 5,000 square feet in size with high ceilings everywhere. The main level features a 19-foot vaulted ceiling. That sounds like a lot to heat. Not so, says Schlesinger. “We expect this house to be heated for about half of what it would cost to heat a regular house this size,” he said, because of the materials used in building and the attention to details. This house will use radiant heat, said Schlesinger, which comes through the floors. “When your feet are cold, so are you,” said Schlesinger. “Radiant heat will keep the house warmer.” All outside air will pass through an electronic filtration system to remove dust, pollen and other allergens. The house itself will be pressure tested for any leaks. The windows are high efficiency Argon gas-filled, with fir interior framing. The foundation walls are poured concrete with rigid foam insulation. Sixteen-inch floor beams are used to create rigid flooring with no squeaks. These beams also provide strength and reduce the number of beams needed from floor to ceiling. Outside, the siding is cement stucco. Solid mahogany wood shutters, which have been recycled, are used for a dramatic effect. Even the three garage doors are made from the recycled mahogany. A recycled wrought iron railing will be sandblasted and used on the property. The copper gutters on the house will direct water to a cistern, which will be used to water the grounds. The roof is Vermont slate trimmed with copper. Local materials A black walnut tree on the property was sent to the mill and will be used for the flooring. On-sight fir trees provided the seven-foot solid interior doors and trim. For health reasons, no PVC piping has been used in the house. Instead a different plastic that gives off no vapors was used. The exterior walls will be sprayed with a light foam, non-volatile and without formaldehyde and then filled with cellulose. There are no hot water heaters. Instead, Schlesinger said, hot water will be heated instantly, saving on energy costs as well. Glenn Rhein has been in the construction business for the past 25 years. His brother, George, has been at it for 30. Their father before them started the business in 1952. Rhein said they decided to go with green building because it’s the way of the future. “There’s just so much waste in construction,” said Rhein. “We just decided this is the way of the future.” Rhein said there are only 12 homes built in New York that are certified green. Building green isn’t the easiest thing to do just yet. “Certified green materials aren’t easy to get,” said Rhein. “Faucets, woodthey are not readily available but it’s getting easier as time goes by.” Part of building green is the proximity of materials. “Buying materials within a 500-mile radius cuts fuel costs and emission,” he added. “Using local contractors cuts down on commuting time. The slate roof will probably last 100 years. It came from less than 500 miles away. An asphalt roof would have to be changed every 20 years. That whole roof goes into a landfill five times compared to the slate roof.” The cost is also an issue. Rhein said that estimates put the cost of a green house at about eight percent higher than a conventional construction. “We’re finding it is a lot more.” Lots of green The first and second floors total 4,200-square feet of living space. The basement also has a finished media room more than 500 square feet. The rest of the basement is cavernous and, with nine-feet high ceilings, could easily be used for living space. The builders are working toward obtaining the Leadership in Energy and Environmental Design certification for their green building, Schlesinger said. Efficiency and beauty don’t come cheap. This home, which is not completed, is listed for $1.6 million. It is the first of six being built just off Amity Road. “This is the first green house I’ve ever been involved with,” said Schlesinger. “I have been involved with lots of builders. These are two of the best builders I’ve ever seen.”